Actuators are used to transform energy received from a pressurized fluid (air or oil) or electrical energy into mechanical energy, usually in linear or rotary motion.
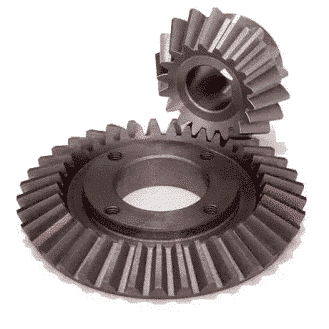
Actuators are used to transform energy received from a pressurized fluid (air or oil) or electrical energy into mechanical energy, usually in linear or rotary motion.
There are three main types of actuators: pneumatic actuators (which use compressed air), hydraulic actuators (which use pressurized oil) and electric actuators. To help you choose the right actuator, we recommend that you consider certain factors.
First, you will need to think about the desired movement. There are two types of movement available for actuators: rotary actuators (which produce a rotary movement) and linear actuators(which produce linear movement). Next, you will need to consider how much torque (if rotary) or force (if linear) the actuator you choose should develop.
Then, depending on your application, you will need to determine whether you need a single-acting or double-acting actuator. This is a specific characteristic of hydraulic and pneumatic actuators, so you won’t have to consider it for electric actuators.
You can choose between a pneumatic actuator, a hydraulic actuator and an electric actuator. Your choice will depend on your application, load and desired speed. For example, hydraulic actuators are chosen for their power as they can carry heavy loads. Pneumatic actuators, on the other hand, are chosen for their speed. It should be noted that electric actuators are not recommended for use in ATEX zones (explosive areas). If you work in this type of environment, we recommend that you choose a hydraulic or pneumatic actuator.
Another factor that should guide your choice of actuator is ease of use. Electric actuators are easy to install and operate. Hydraulic actuators, on the other hand, are the most difficult to operate and require significant maintenance.
If you are looking for an easy-to-use actuator, we recommend choosing an electric actuator. This type of actuator is particularly effective if you have applications that require managing multiple positions. They manage positions very precisely, with a margin of error of 0.001 mm.
They can also support very heavy loads, up to several tons. But while electric actuators can support heavier loads than pneumatic actuators, they cannot support as heavy loads as hydraulic actuators.
Another advantage of electric actuators is their high and precise speed. These actuators also pollute less and are more quiet.
However, before purchasing an electric actuator, we recommend that you consider several important factors. First of all, the movement of the axis of your electric actuator can be powered either by an asynchronous motor (robust and easy to implement), a stepper motor (precise) or a brushless motor (long life expectancy, but very expensive).
Secondly, as mentioned, it is strongly discouraged to use an electric actuator in an ATEX zone. This is because ignition can trigger an explosion or fire. If you work in this type of environment, we recommend a pneumatic actuator (with a compressed air supply) or a hydraulic actuator.
A pneumatic actuator converts pneumatic energy (compressed air) into mechanical energy. A distinction can be made between linear and rotary actuators.
As pneumatic actuators are powered by compressed air, they limit the risk of explosion and fire by not using ignition. They are also frequently used in automated industrial systems. Being powered by compressed air makes pneumatic actuators very fast; which means they are very practical for high-speed applications.
Pneumatic actuators are also the most popular devices. They are inexpensive and have a long life expectancy. They are also easy to install. However, we recommend that you pay attention to the quality of the compressed air. Poor air quality can damage the actuator.
The supply pressure of a pneumatic actuator is generally estimated at 6 bar. Its pushing and pulling force depends on the size of the bore. The speed of pneumatic actuators is high, between 0.2 and 0.3 m/s. They also have a theoretical thrust between 20 N and 50,000 N, for a pressure between 4 and 8 bars. Nevertheless, their force is lower than that of hydraulic actuators.
Another important advantage of pneumatic actuators is that they are lightweight and space-saving.
Hydraulic actuators are powered by a liquid fluid (oil). Since this fluid is incompressible, this type of actuator can support higher forces than pneumatic actuators. They are therefore ideal for heavy loads. By regulating the flow of fluid entering the cylinder chambers, it is easier to regulate the speed than with a pneumatic actuator. Lastly, these devices have a long service life.
Hydraulic actuators have a lower speed of action than pneumatic actuators however. Oil leaks can occur, which can result in a decrease of efficiency, especially since the circulation of the fluid in the pipes generates pressure losses. High pressures (between 50 and 700 bar) also increase the risk of accidents and the flammability of oil can increase the risk of fire. Lastly, it is expensive technology as both the components and preventive maintenance are expensive. We recommend that you pay close attention to the maintenance of your hydraulic actuator, especially the seals that protect the cylinder chambers.
The main difference between a single-acting actuator and a double-acting actuator is the way the actuator returns to its original position. This technology concerns hydraulic and pneumatic actuators.
In a double-acting actuator, pressure must be applied alternately to each side of the piston for the actuator to move in either direction. In a single-acting actuator, a spring is interlocked and allows the actuator to return to its original position.
The choice of a single or double-acting actuator should be made according to your application. Double-acting actuators can be used in machines that exert force in both directions (such as overhead cranes). These more flexible actuators allow for adjustable end-of-stroke cushioning, as well as easier speed control. However, this technology is more expensive than single-acting actuators.
Single-acting actuators are generally used for lifting machines with poles. They are more economical and consume less fluid than double-acting actuators. However, they are cumbersome and have limited range.