A rotary encoder is a device for obtaining angular position information for motion control applications. The information collected concerns angular velocity, position, displacement, direction or acceleration.
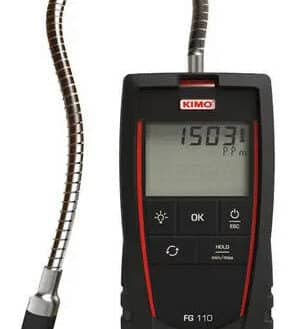
A rotary encoder is a device for obtaining angular position information for motion control applications. The information collected concerns angular velocity, position, displacement, direction or acceleration.
When choosing a rotary encoder, you should first determine whether you should use an incremental encoder or an absolute one.
• An incremental rotary encoder provides pulses according to the rotation of the axis. A pulse or increment is a square digital signal. The encoder resolution corresponds to its number of increments per revolution It must be reset each time the power supply is interrupted.
• An absolute rotary encoder integrates its own counter, in the sense that it saves the last value recorded if the power supply is interrupted.
An incremental rotary encoder is more affordable, but you should choose an absolute rotary encoder if:
• Resetting the rotary encoder is detrimental to your application;
• Your signal processing system may be disturbed by noise that could generate false pulses;
• There is a high risk of not counting pulses (for example at high frequencies);
• The rotary motion is oscillating and does not correspond to a complete rotation;
• It is important to know the real position of the axis at all times;
• It is necessary to count the number of revolutions completed. In this case, you should select a multiturn absolute rotary encoder.
When choosing a rotary encoder, you should also determine the size according to the system it will be integrated into. You will need to determine its space requirement, that is the housing diameter and length as well as the diameter of the output shaft (whether solid or hollow).
Finally, it will be necessary to identify the environmental and mechanical constraints that the encoder will have to face in order to choose the appropriate level of protection.
The incremental rotary encoder measures an angular displacement with respect to a reference position. After a power failure, the data processing system must wait for the encoder to send the information corresponding to the reference position in order to correctly exploit the angular displacement information.
Incremental rotary encoders are designed using different technologies, each with its own advantages and disadvantages. The most common technologies used are:
• Optical incremental rotary encoders: these encoders use light-emitting diodes (LEDs) to “read” the angular displacement. These rotary encoders are affordable and offer high resolution (high precision). This technology is widely used in industry, but the optical scanning system can be disrupted if the environment presents a risk of corruption (dust, oil, etc.).
• Magnetic incremental rotary encoders: the pulses are emitted by magnets. This technology is also commonly used in industry because magnetic encoders are less subject to the risk of fouling.
Regardless of the operating principle of the rotary encoder, the output signal is a series of pulses that make up a binary code, i. e. a succession of 1 and 0 corresponding to the angular displacement, depending on the encoder’s resolution. This signal can be used to determine the direction of travel, the value of travel in relation to the reference position, the speed or the acceleration.
With an incremental encoder, you can connect the encoder wires to the inputs of a PLC. Which inputs you should use are determined by the encoder’s operating frequency. This frequency is proportional to the rotational speed of the axis and the resolution of the encoder. In the case of a high frequency, the signal corresponding to the reference position is used to correct counting errors for certain pulses that aren’t taken into account.
Generally, a rotary encoder has 5 to 12 outputs (wires or connector terminals), which must be connected to a counter. In the case of an encoder with 5 outputs, two wires are used for the power supply and the other three to send the signals corresponding to the angular displacement.
An absolute rotary encoder indicates an angular position as soon as it is switched on. It continuously delivers a signal that corresponds to the real position of the axis to which it is connected. There are two types of absolute encoders:
• A single turn rotary encoder indicates the position of the axis. The value sent by the encoder is the same for each revolution. A simple single-turn rotary encoder makes it possible to know the position of the axis at any time (even when stationary), in addition to information related to angular displacement.
• A multi-turn rotary encoder integrates secondary rotary encoders to indicate the number of revolutions performed in addition to the position of the axis.
As with incremental rotary encoders, the technology mainly used for absolute rotary encoders is optical which offers a high level of accuracy, but may be sensitive to a risk of corruption from dust, oil, etc., and magnetic.
With an absolute rotary encoder, the axis position is defined by a unique code that is sent as soon as the encoder is powered on. It can be operated as is or transformed to be transmitted as a digital signal through a fieldbus system such as SSI, CANopen or Profinet.
The resolution of a rotary encoder corresponds to the maximum number of points it can measure over a revolution. For an incremental rotary encoder, the resolution is directly linked to the number of pulses it delivers per revolution. For an absolute rotary encoder, it is linked to the number of bits coding is performed on. For example, a 16-bit encoder will have a resolution of 65,536 dots per revolution.
You should choose an encoder resolution that will meet the requirements of your application and the accuracy of the mechanical components that form the measuring chain. The encoder is connected to an electronic device, controller or counter, which has a maximum input frequency that must be respected. A high-resolution incremental encoder provides a greater number of pulses over a revolution than a low-resolution incremental encoder. Depending on the rotational speed imposed by the application, the encoder output signal may have a higher frequency than the device connected to the encoder is able to handle. In this case, you will need to use a rotary encoder with a lower resolution.
Assembling a rotary encoder depends on its form. It is therefore important to determine how the rotary encoder will be connected to the axis to be measured.
There are three main types of assemblies:
• A rotary encoder with a solid shaft that can come in different shapes such as a truncated cylinder, square or hexagon. This type of encoder can be mounted at the end of a hollow axle or, for example, in a gear pinion.
• A rotary encoder with a hollow shaft, in which an axle can be inserted.
• A rotary encoder in two parts. This includes a disc that is mounted at the end of the axis and a “pick-up head” that will be fixed above the disc.